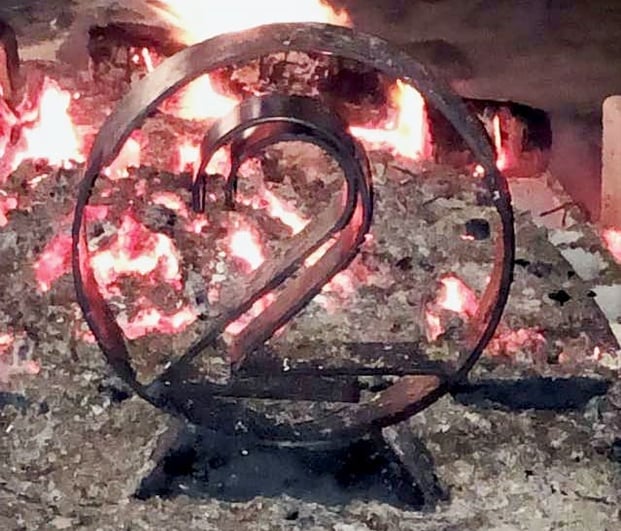
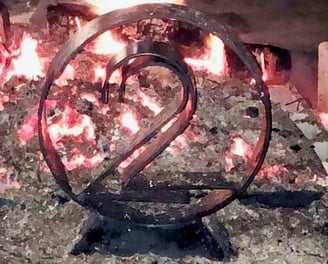
Artistic Forging Project
My fascination with the forging course during my first year at Arts et Métiers Institute of Technology sparked a keen interest in pursuing a project in this field. As an extracurricular endeavour, I collaborated with three classmates to design and craft a unique metal structure. Ingeniously constructed, this piece exhibits the number '2' when viewed from the front and transforms into the number '1' when observed from the side.
CAD Design
Initially, we collated various design ideas from our classmates to craft an aesthetically pleasing concept. Subsequently, we refined this design to align with the capabilities of our available machinery, and to ensure sufficient thickness for durability, especially considering its intended placement in a brazier, as illustrated in the first picture of the page.
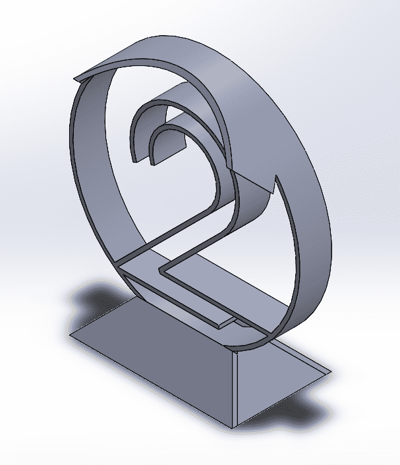
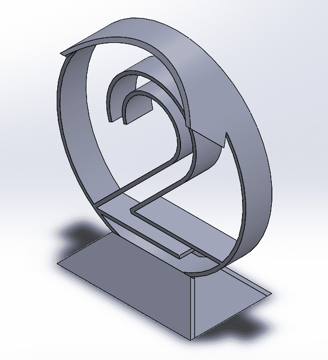
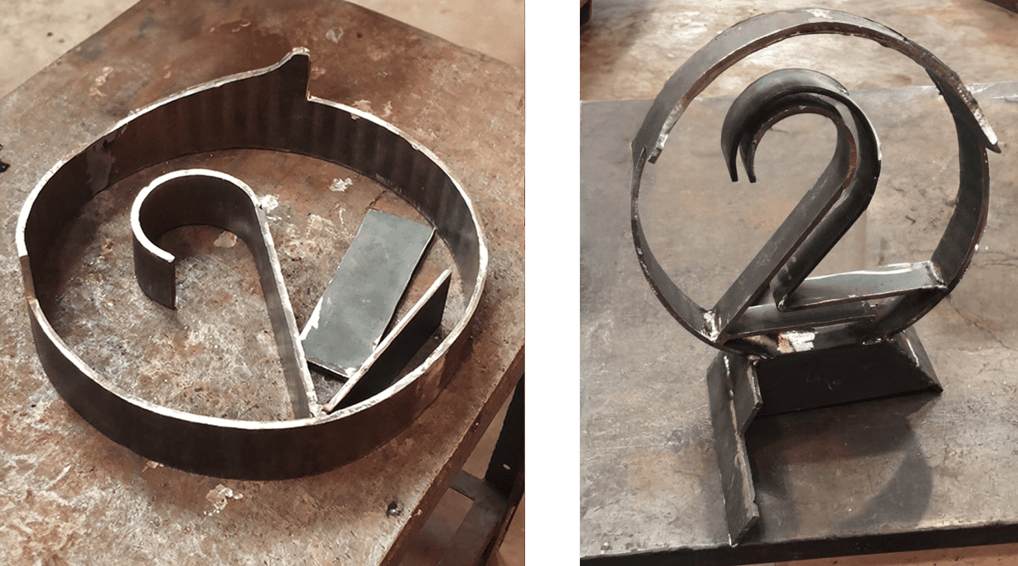
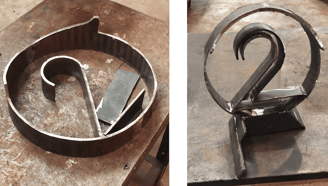
Fabrication Process: Shaping & Assembling The Metal Structure
In the fabrication stage of our project, we first utilized precision plasma cutting to create the intricate shapes outlined in our design. Following this, each piece was carefully bent to the correct angles using a cornice brake, a step that demanded both accuracy and a deep understanding of metalwork. The final assembly was achieved through meticulous TIG welding, ensuring not only the structural integrity but also the aesthetic appeal of the piece. This careful process of cutting, shaping, and welding showcased our attention to detail and commitment to quality, resulting in a metal structure that perfectly embodied our initial vision.
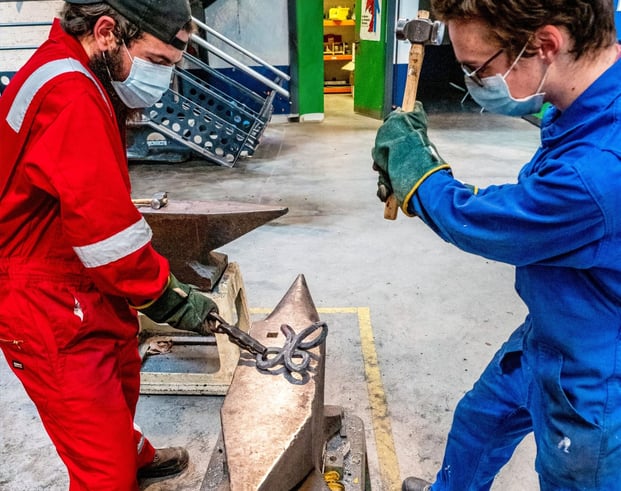

Blacksmithing
Embracing blacksmithing as a hobby, I joined the blacksmithing club at my school, starting with no prior experience in the craft. My journey began with straightforward projects like forging a knife, which served as a foundation for learning. As my skills and confidence grew, I progressively took on more complex and ambitious blacksmithing projects.
Forging A Symbol: The Four-leaf Clover
In a collaborative effort with two friends, I embarked on the challenge of forging a four-leaf clover, a symbol emblematic of my school, from a thick steel bar. This project was a significant learning experience, particularly in mastering heat control. The necessity of heating the bar to a malleable red-hot state, while cautiously avoiding overheating or burning the metal, greatly enhanced my skills in precise temperature management.
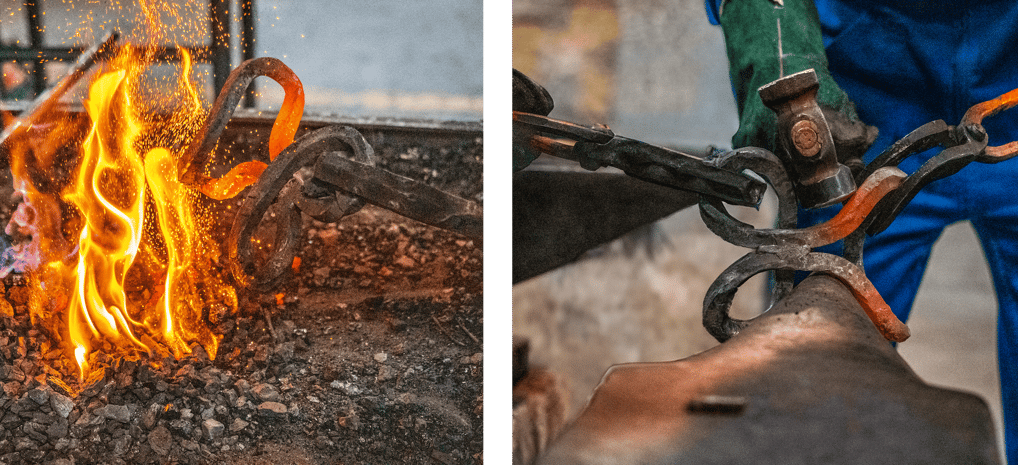
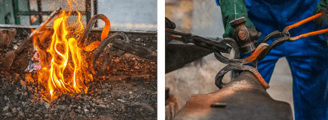
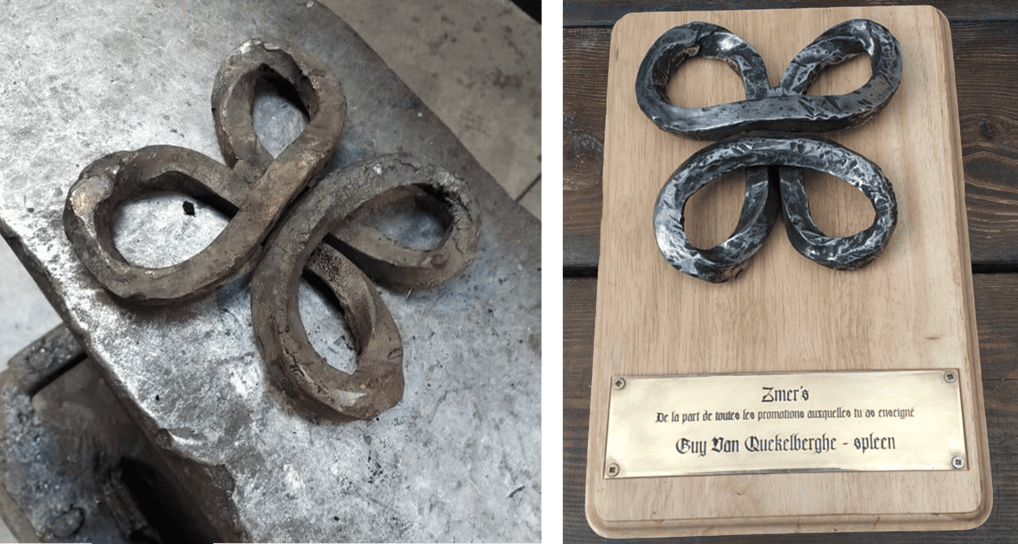
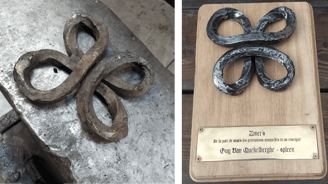
Final Touches & Presentation
After some meticulous finishing touches, the clover was finalized, transforming into a symbol of appreciation and respect. This handcrafted piece, a blend of skill and dedication, was then proudly presented as a farewell gift to a retiring teacher, symbolizing gratitude.
Initiation Into Blacksmithing: Knife Forging
My journey into blacksmithing began with my first project: forging a basic knife from a steel bar. This endeavour was a true eye-opener, revealing the complexity and skill required in forging. It taught me that achieving proficiency in this craft demands considerable practice and dedication.


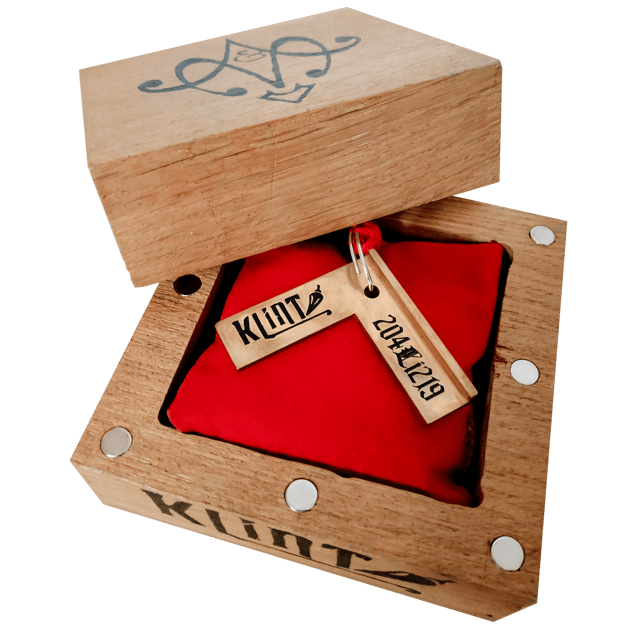
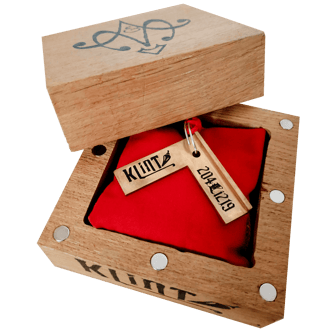
Crafting A Legacy: Square Pendant Project
In line with our school's tradition, each student creates a unique, engraved square pendant. For this project, I played a pivotal role, overseeing the entire machining process for the production of these pendants. My responsibilities involved managing the transformation of brass bars into the preliminary shapes for 170 pendants, ensuring that each classmate's vision for their pendant was brought to life.
Brass Milling Process
The majority of our machining tasks were accomplished using milling machines. Initially, we utilized a conventional milling machine to reshape the long parallelepipedic brass bars into L-shaped forms. Subsequently, these bars were precisely segmented into individual pendants using a CNC machine, ensuring accuracy and consistency in each piece.
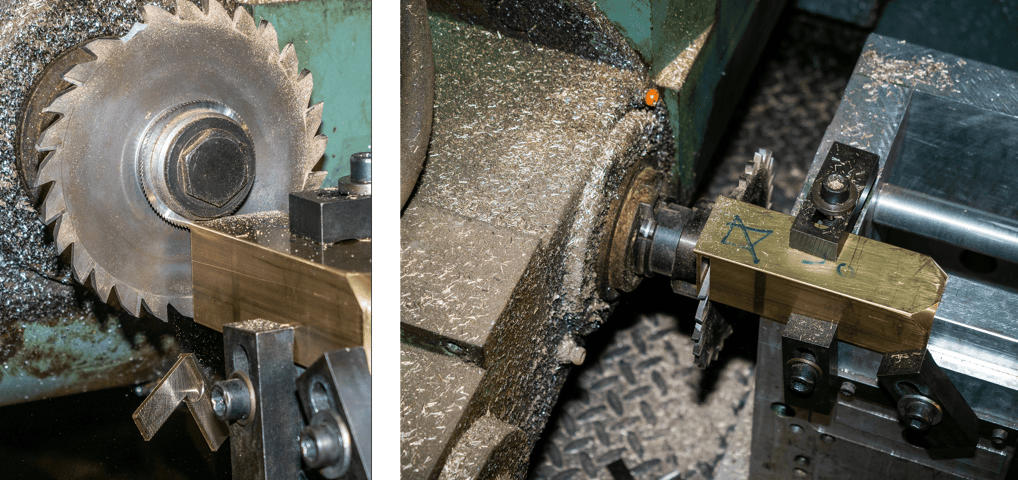
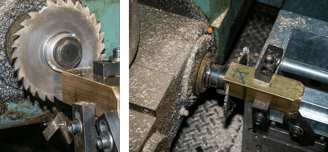
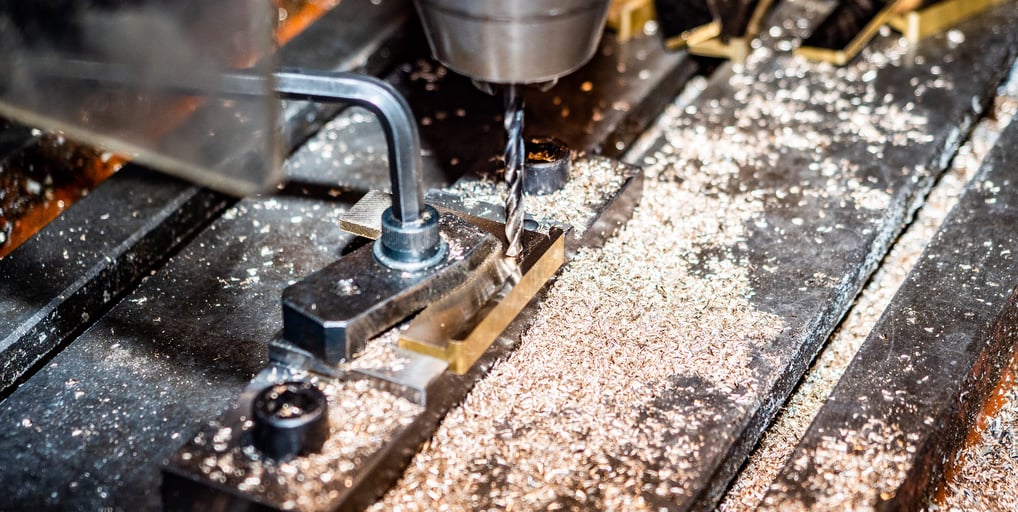
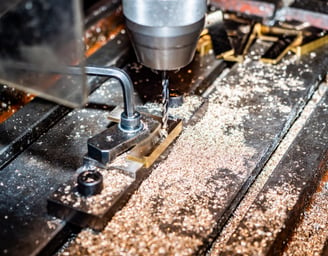
Detailing Process: Drilling
The next step in our process involved using a drill press to meticulously create holes in each square pendant. This was a crucial task to ensure that the pendants could be properly fitted onto a necklace upon completion.
Filing And Replication
The last step of my responsibility entailed carefully filing each pendant to smooth out any sharp edges, ensuring a refined and safe finish. This process was systematically repeated until approximately 200 pendants were produced (the 170 required, and additional ones as safety stock). With my tasks in the workshop completed, each classmate then collected their pendant to proceed with the final finishing work.
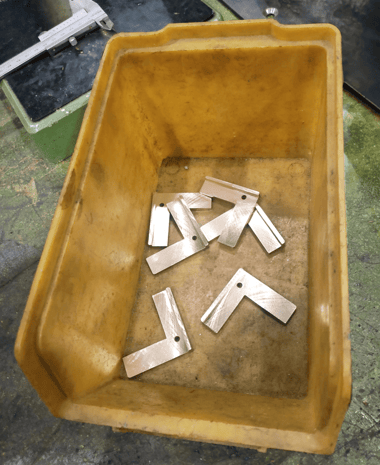
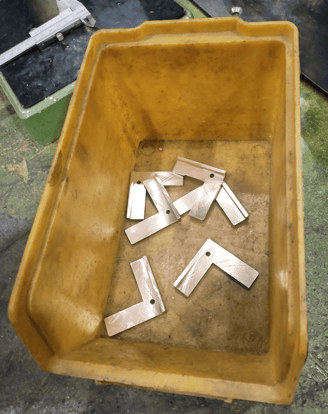
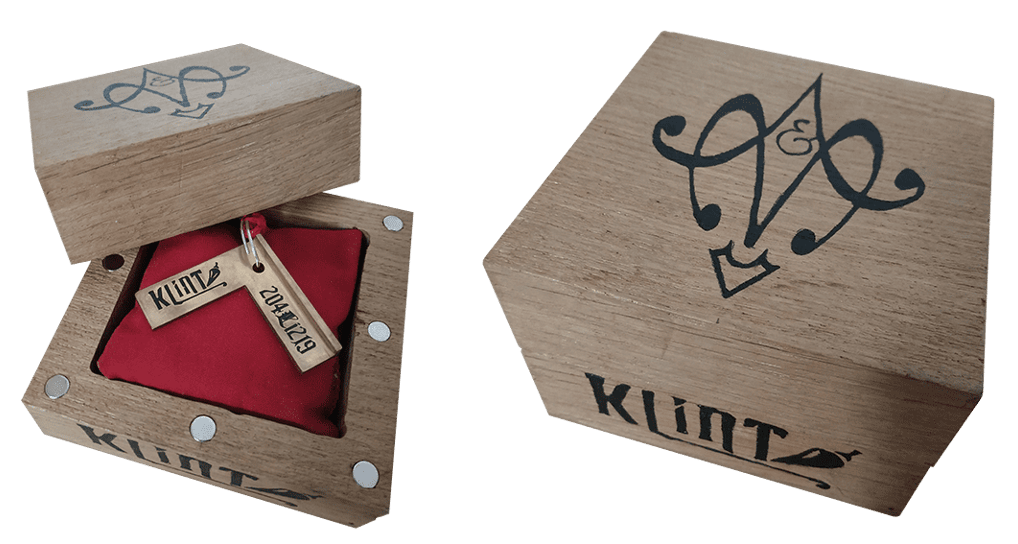
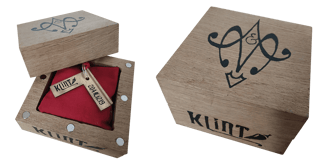
Crafting The Display Box
Following the sanding of the pendant, I proceeded with the chemical etching process and then carefully filled the etched designs with paint for enhanced visibility. To complement the pendant, I crafted a bespoke display box with a magnetic closure, skillfully carved from a single block of wood. This box also included a small cushion, providing an elegant and secure presentation for the pendant.