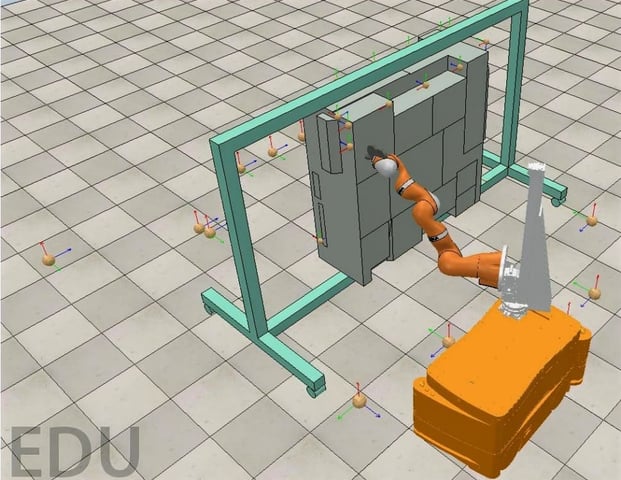

Robotic Project
Inspired by a pioneering study from Safran, this project explores an innovative approach to quality control aimed at augmenting testing capabilities and ensuring the reliability of products. Central to this initiative is the integration of collaborative robots, designed to operate seamlessly alongside human operators within the same workspace.
Context
At Safran Aerosystems, the assembly process of an electrical relay necessitates a manual inspection of each component by an employee prior to installation in an aircraft. The objective of our project is to develop a robotic solution that autonomously performs this verification using a camera. Utilizing a KUKA robot, our task involves designing a robotic arm that can efficiently and effectively inspect the entire board.
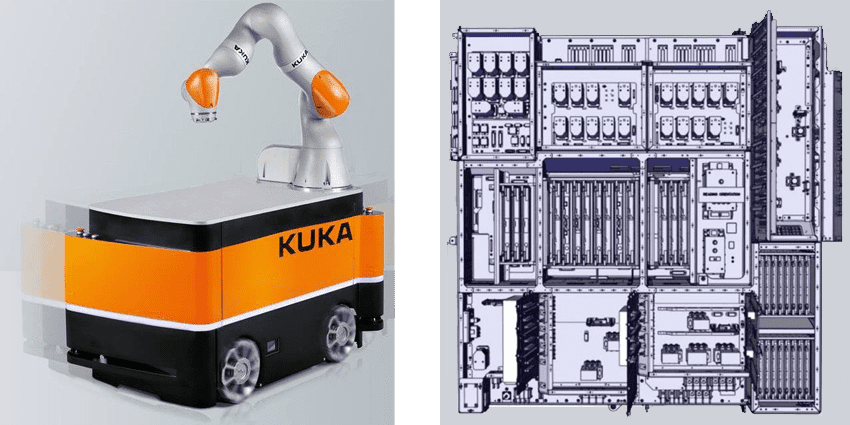
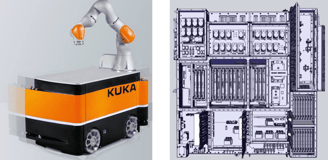

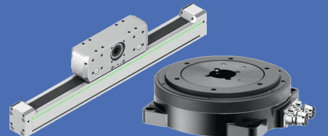
Sizing & Selection Of Components
In the process of developing our robotic system, we need to meticulously size and select appropriate components, including existing linear axes and rotary tables. This involves determining the specific references that best align with our project requirements, ensuring an optimal match for our design needs.
Design Of Structural Connectors
In order to assemble the various components of our robotic system, from the moving platform to the camera, we focused on designing structural connectors. These connectors were specifically engineered to withstand the dynamic forces of the robot's movements, ensuring they are robust enough to maintain stability and functionality under operational conditions.
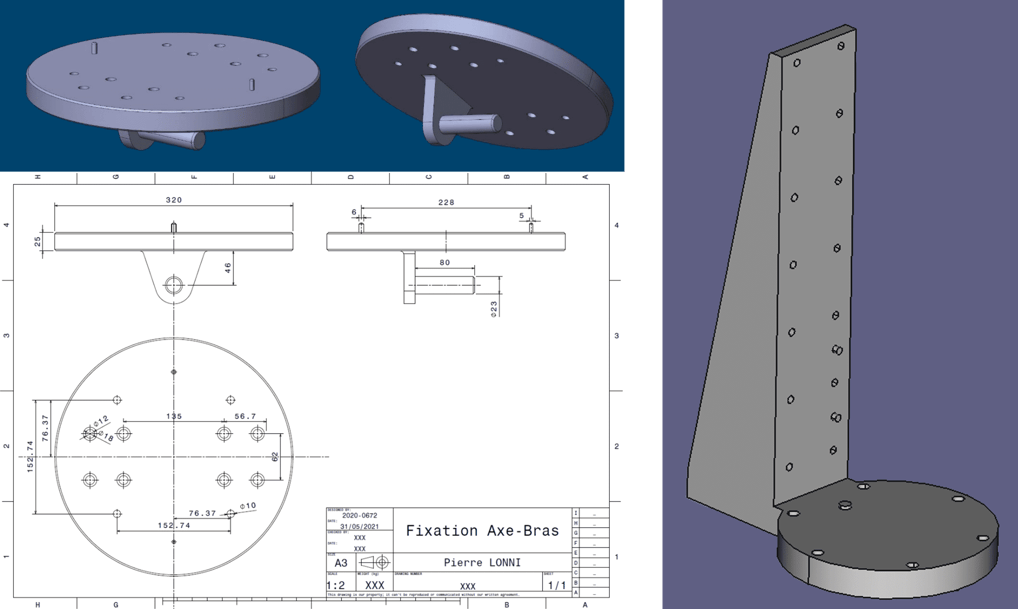
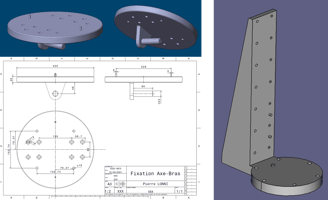
Simulation Of Robotic Range And Motion
To verify the operational range of our robot, I created a simulation using CoppeliaSim. This simulation was instrumental in demonstrating the designed system's movement capabilities, ensuring it can effectively reach all necessary positions for optimal functionality.