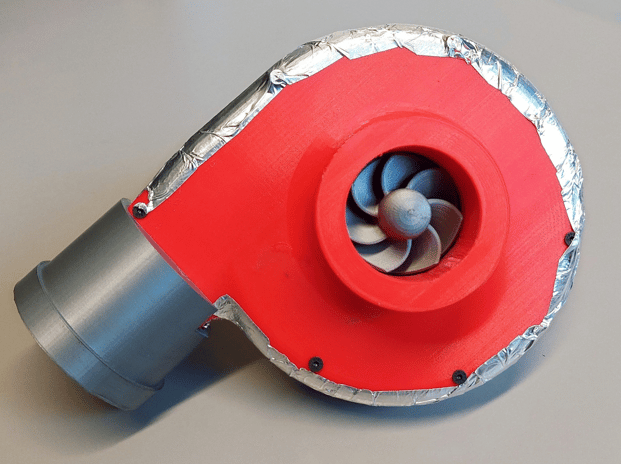
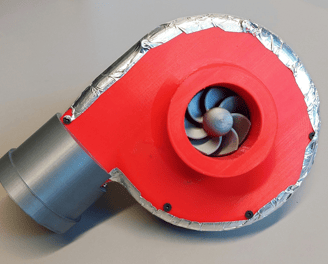
Turbocharger Design
This project involved the comprehensive design of a turbocharger for a hydrogen car, with a focus on optimizing air supply to the fuel cell. This challenging task encompassed all stages from initial dimensioning to final testing, carried out with limited guidance from our professors, emphasizing our self-reliance and technical skills.
Technical Layout
Utilizing advanced hydrodynamic and hydrostatic analyses, we accurately determined the essential specifications for the rotor. Leveraging these specifications, we employed a Python program to generate a detailed technical layout. This program also facilitated the creation of precise guiding curves, which served as foundational elements for our subsequent CAD modelling.
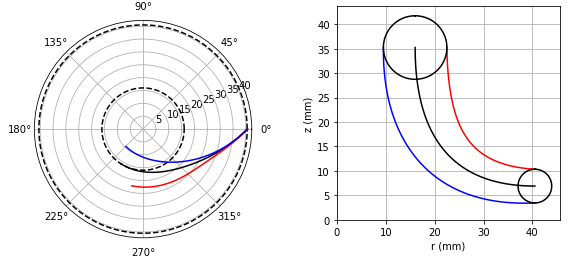
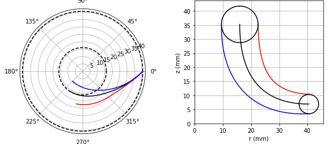
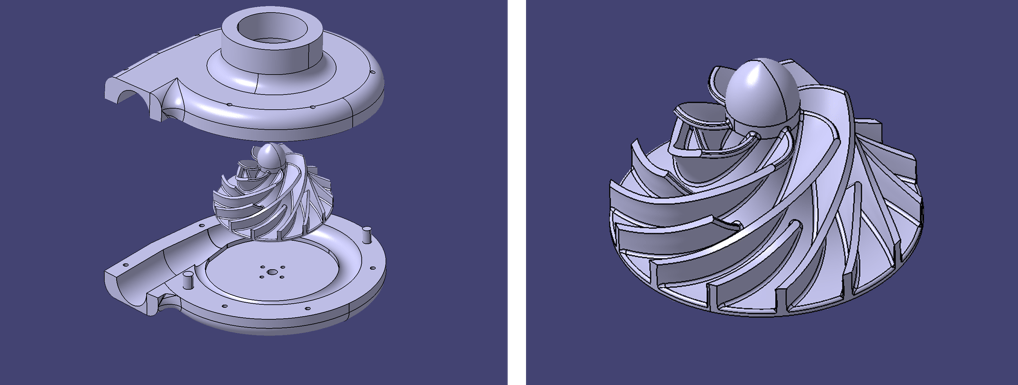
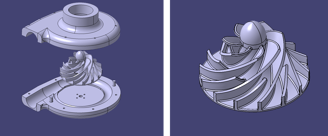
CAD Design
For the 3D modelling of our rotor and volute, I employed Catia software. This task required intricate work in both the surfacing and solid modelling workshops to accurately render the complex curved geometries. This process was pivotal in bringing our technical designs to life in a detailed and precise 3D format.
CFD Simulation
I conducted a comprehensive CFD analysis using Star-CCM+ by creating a 3D model of the fluid volume. This critical step enabled us to analyze the results in depth, ensuring that our design adhered to the specified requirements.
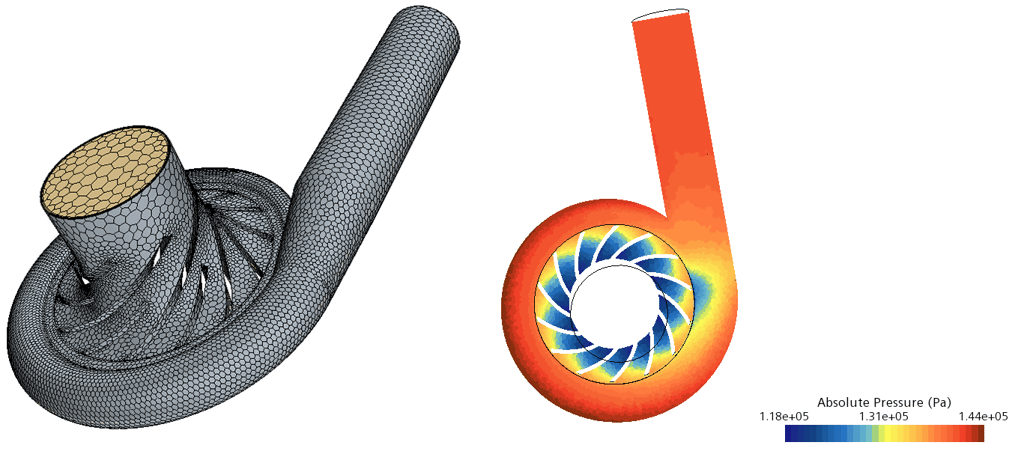
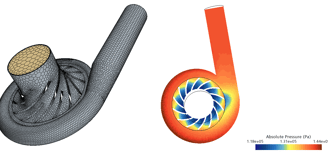
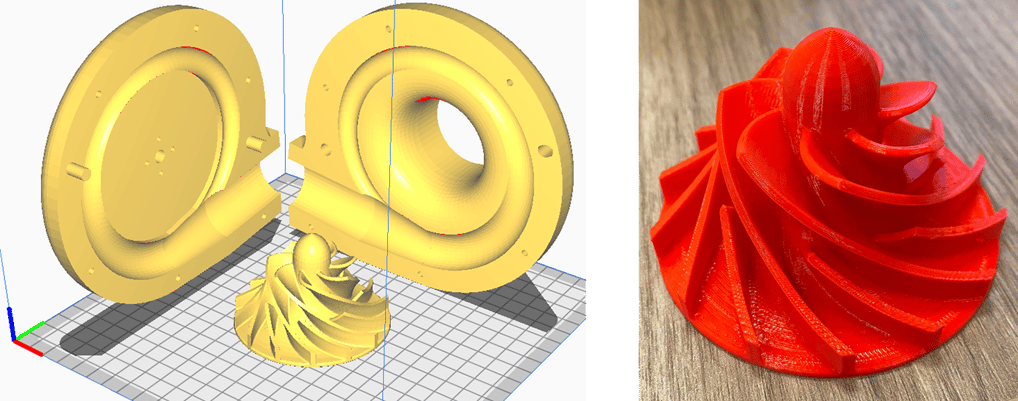
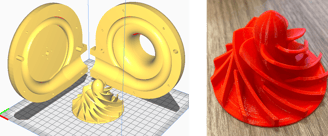
3-D Printing
Subsequently, we 3D printed the rotor and housing components to enable real-life testing. To enhance the parts' quality, additional machining was necessary due to the 3D printer's limitations in achieving optimal surface finish.
Practical Testing
In the final phase, we conducted practical tests on our design using a test bed supplied by our professor. Our robustly designed rotor, despite being crafted from plastic, demonstrated the capability to rotate at high speeds. The tests yielded satisfactory results, marking the culmination of our successful project.
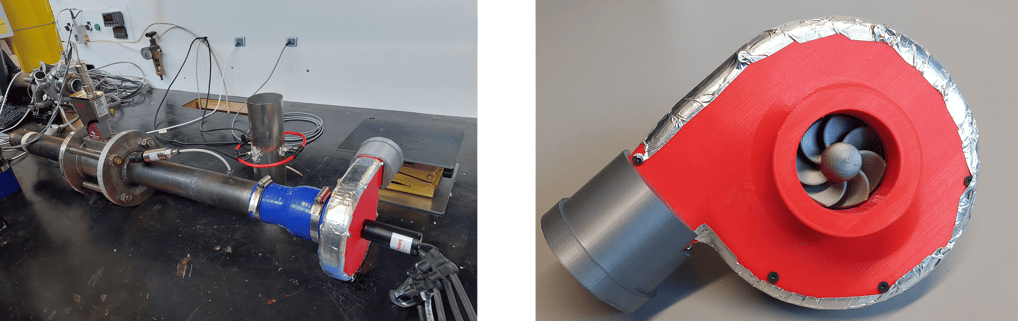
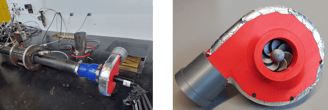